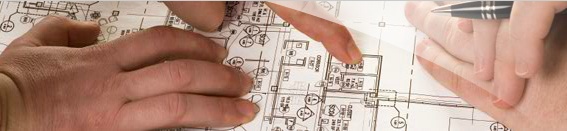
In the current situation with COVID-19 federal and regional governments have imposed a number of generic safety requirements, but have provided no specific details for organizations attempting to implement them. This leaves most people responsible for implementation bewildered as to how to make it happen where it counts, in the restaurant, the factory, the warehouse, the school, the hair salon, etc.
Safety Analysis fills the gap. Much work that is currently not well defined because of this uncertainty needs to take place at the level of the facility, by people who have first-hand knowledge, in detail, of:
- The facility itself, i.e. its layout, including the position of everything inside, rooms, equipment, storage tanks, supplies, etc.
- The customers, associates and personnel who will be within it when work resumes.
- The means of getting them, supplies, and finished goods in and out of the facility, as well as through it, e.g. parking lots, doorways, hallways and corridors, etc.
- The nature of the work that will take place there.
- The interaction that typically takes place between customers, associates and other personnel as that work is conducted.
Of paramount importance in all of this is the idea that things, and often people too (we call them customers, clients, patients, etc.), get processed as work is conducted. Raw materials enter a plant and are refined, parts are joined into assemblies, whole chickens are broken down into portions, cars are serviced, and customers come into a shop and are accommodated,. Work flows as these things take place. A chain of people, usually with machines mixed in among them, each add a little more value what traverses the flow as they execute their work. Out of the end comes a product or service that ideally meets its needs perfectly.
Safety Engineering is the process of capturing and studying this flow of work, and generating a way in which to make it work safely, by generating a plan for ensuring that it never, ever hurts anyone, either as they execute the process, or use the product or service that comes out the end.
This plan captures the low-level details that are missing in the directions from above. It is important that, as they are filled in, they must mesh fully with those requirements put forth by the authorities.
Think of the result as a large ‘tree’, with many branches, each of which describes how to achieve safety in a greater level of detail. To the implementer this tree is oriented upside-down with its trunk pointed upward. In Safety Analysis we capture safety requirements in such trees, however we call them by the fancy name ‘requirements hierarchies’. Each high-level safety requirement
Careful management of Safety Requirements is important. It is the most detailed and benefits greatly when persnickety people conduct it. Why is this? The devil is in the details. Once a complete set of safety requirements is in hand it is imperative that every last one be met — missing even the smallest detail means that someone will get hurt, if not immediately then eventually.