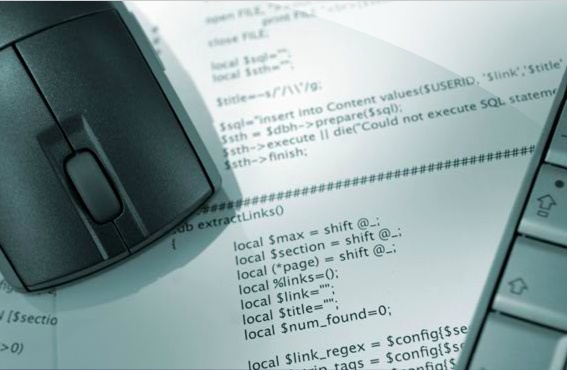
Functional Safety is safety captured in instructions. Instructions for operating a machine, instructions for driving a car, directions for assembling a bicycle. These instructions can be written in a natural language, like English or Japanese, and executed by humans, or captured in software code to be run on a computer.
It is safety in design and execution:
- Execution controlled most often by software, programming or, for humans, via work-, assembly- or process-instructions,
- directing actions of and movement within and by, devices, products, equipment, machinery, and/or people,
- which could be harmful to people, animals, pets, or the environment,
- if not monitored for the appearance of hazards, which are most often failures in computing, interface, sensing, actuating hardware, wiring and cable, or a failure to follow instructions,
- but could be other sources of harm, such as the COVID-19 virus or other natural phenomena,
- or in the development of software (bugs), or those instructions.
As opposed to safety in design and construction, which is:
- safety of parts, components, and assemblies, and
- the devices, products equipment, machinery, and facilities made from them,
- ensured primarily by considering carefully the characteristics of materials used,
- in order to safely accommodate their strengths and weaknesses.
Techniques and methods for ensuring safety in design and construction are associated with, and specifically taught to students of, traditional engineering disciplines including civil, mechanical, electrical and electronic engineering. Practitioners within these disciplines inherently study failure conditions, failure modes and mitigation of failures as a core part of their curriculum.
Those for ensuring safety in execution have traditionally as well — until the advent of software. This is because software never fails, i.e. it always executes the instructions it captures precisely and identically each time, and never fails to do so. Because of this software engineers, and those who create work instructions, are often not adequately trained in how to handle failures, and how to anticipate, to detect, and to compensate for them.
For this reason Functional Safety is a necessary and useful concept in safety analysis, and the development and deployment of safety solutions.
International Standard ISO-26262 encapsulates an approach for designing and deploying Functional Safety in electronics used in Automotive applications. There are also several others which cover Off-Highway, Aerospace, Rail and Consumer Products. All have been written to help keep people safe.